Technical info
There are many different types of pliers for a great variety of different applications.
Pliers can be distinguished by their function. They can be used for gripping and holding but also for cutting, twisting, pinching, stripping and shaping. Some pliers are multifunctional.
Pliers are reliable tools for work, hobbies and for household tasks.
If the only tool you have is a hammer, every problem looks like a nail.
Abraham Harold Maslow
In most cases, pliers can be split into three areas: The grip/handle, the joint and the head. Pliers operate on the basis of the lever principle. The joint forms a moveable link between two double-sided levers. The longer grip area is the lever arm (force arm) and this exerts a force on the shorter lever arm (load arm) with the head of the pliers.
High strength, low wear and the desired surface hardness are achieved through the surface treatment of the steel components. In doing so the material remains tough.
The surface characteristics can be influenced through heat treatment and the use of coating and alloying elements. The following illustrations show the surface treatments possible for the 120 mm flat nose pliers, as an example. With serration = gripping surface with transverse grooves. Without serration: Gripping surface polished smooth.
Flat nose pliers 120 mm
- Surface: Mirror polished
- 2 springs
- Without serration
- Grip design: Blue PVC
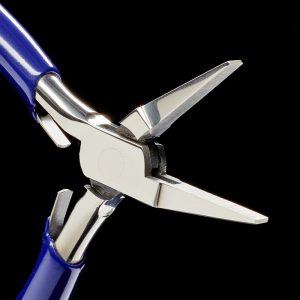
Flat nose pliers 120 mm
- Surface: K 180, polished (standard)
- Without springs
- Without serration
- Grip design: Blue PVC
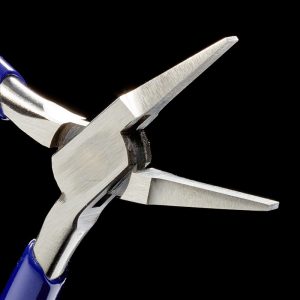
Flat nose pliers 120 mm
- Surface: Finely polished and blasted
- With springs
- Without serration
- Grip design: Blue PVC
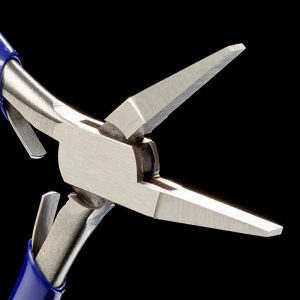
Flat nose pliers 120 mm
- Surface: Nickel-plated
- Without springs
- Without serration
- Grip design: Blue PVC
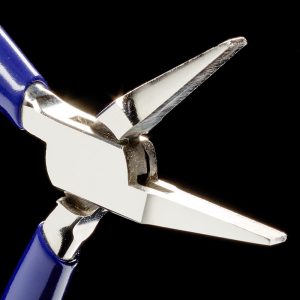
Flat nose pliers 120 mm
- Surface: K 180, polished (standard)
- 2 springs
- With serration
- Grip design: Blue PVC
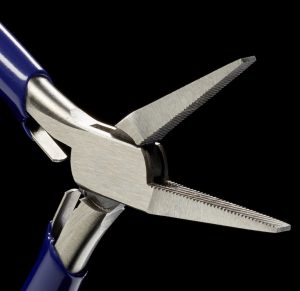
Flat nose pliers 120 mm
- Surface: K 400, fine polished
- 2 springs
- Without serration
- Grip design: Blue PVC
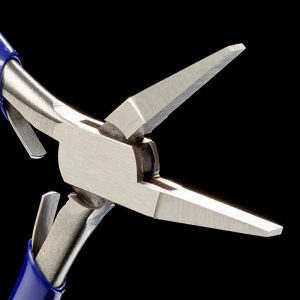
Flat nose pliers 120 mm
- Surface: K180, completely polished
- Without springs
- Without serration
- Grip design: handles completely polished
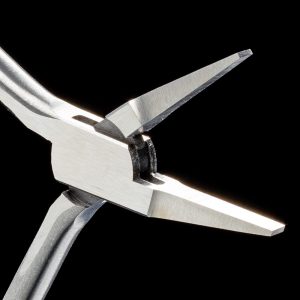
Flat nose pliers 120 mm
- Surface: black gun coating
- 2 springs
- Without serration
- Grip design: Blue PVC
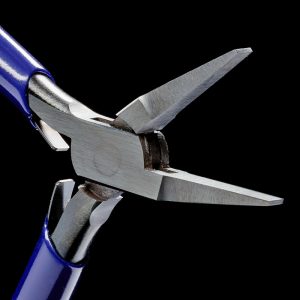
Flat nose pliers 120 mm
- Surface: K 180, polished (standard)
- Without springs
- Without serration
- Grip design: Single-component (grip)
![]() | Box joint: One of the handles of the pliers is fed through an opening in the 2nd handle of the pliers. The mouth of the pliers is precisely aligned and overlapping of the jaws and cutters is prevented even with extremely heavy-duty use. This type of joint guarantees a long service life with no play and easy movement. The pliers will continue to work even when the pivot pin is worn. Manufacturing is more difficult. |
![]() | Lap joint: A simple, standard quality with hardened riveting. Here, the two handles of the pliers are laid on top of one another and joined together with a link pin. Manufacturing is easier. |
Chain nose pliers (semicircular jaws) | |
Round nose pliers (round jaws) | |
Ring bending pliers | |
Flat nose pliers (flat jaws) | |
Bending pliers, one jaw round, one jaw flat | |
Bending pliers, one jaw is flat, one jaw is convex | |
Bending pliers, one jaw concave, one jaw convex | |
Bending pliers, one jaw concave, one jaw round |
The bevel – also known as the grind of the cutter – is a larger or smaller chamfer of the cutter. This machining increases the durability of the cutting tool. Bevels are primarily machined into the jaws of side cutters.
![]() | Large bevel >The more acute, pronounced cutting angle ensures reduced cutting force and thus delicate cutting. Universally applicable for hard and soft steel wire as well as soft materials such as copper wire or cable. |
![]() | Small bevel >Fast flush cut with fine cutting edges. Can be used on soft steel wire, copper wire and cables. Slightly shock-reduced cut on sensitive electronic components. |
![]() | Without bevel >Absolutely flush cut with extremely sharp cutting edges. Can be used on soft steel wire, copper wire and cables. Largely shock-reduced for highly sensitive electronic components. |
Notice:
The life of the cutting edges depends on the angle of the bevel. The sharper the cutting edge, the faster it wears out. Therefore, the service life of pliers with a pronounced bevel is greater than those with a small bevel or no bevel. If a flush or largely shock-reduced cut is not required during use, the use of pliers with a bevel is recommended.
1. Polished grip
The simplest and oldest type of grip is the “polished surface” – with no additional wooden or plastic gripping elements. As a result the complete tool can be cost-effectively produced and the grip can be furnished with the same surface treatment as the head of the pliers. A polished surface has the advantage of simple and thorough cleaning or disinfection.
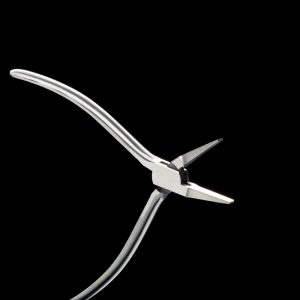
2. Polished grip with ground notches
In addition to the “polished” surface treatment, this type of grip is also furnished with ground notches for extra grip thus enabling more secure handling of the pliers.
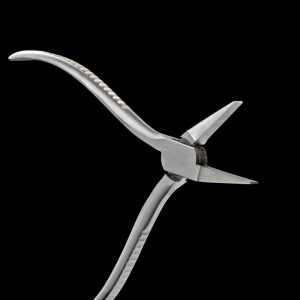
3. PVC-coated grips
Our pliers are available with PVC-coated, non-slip grips. These grips have several advantages: They are easy to handle and save space when stored. Manufacturing is also easier and cheaper than with the multi-component handles – with similar mechanical characteristics. These grips are applied to a heated tool in a dipping process.
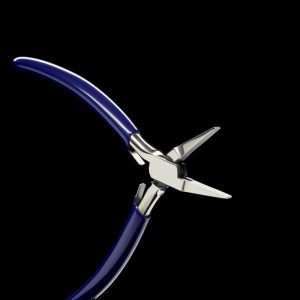
4. Single-component handles
These handles have characteristics similar to the multi-components handles – but are made of only one material.
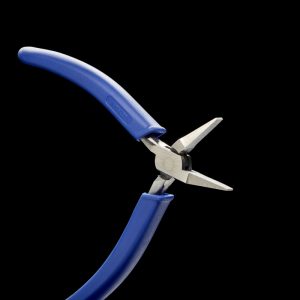
5. 2-component handles
These handle variants are advantageous if the same pair of pliers will be used for several hours and they can also be designed with individual colours. Hard and soft ergonomic grip zones are arranged in the plastic thus preventing pressure points when being held in the hand. They operate like a shock absorber, if hard materials must be cut with a sudden cutting action.
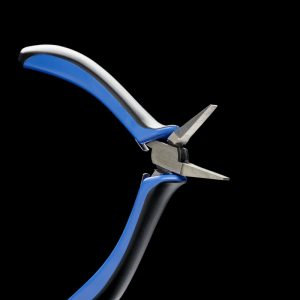
6. ESD handles
One special variant is the electrostatically conductive ESD handles. They are used for pliers that are used to work with electronic components. Electrostatic discharge can cause permanent damage to electronic components. This can be prevented through the very low resistance, conductive constituent parts in the handle material.
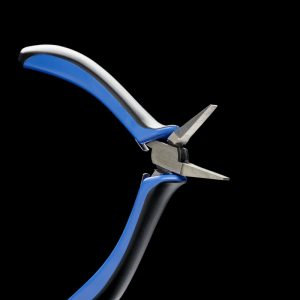